Abstract
Purpose
This papers aims to study lattice structures in terms of geometric variables, manufacturing variables and material-based variants and their correlation with compressive behaviour for their application in a methodology for the design and development of personalized elastic therapeutic products.
Design/methodology/approach
Lattice samples were designed and manufactured using extrusion-based additive manufacturing technologies. Mechanical tests were carried out on lattice samples for elasticity characterization purposes. The relationships between sample stiffness and key geometric and manufacturing variables were subsequently used in the case study on the design of a pressure cushion model for validation purposes. Differentiated areas were established according to patient’s pressure map to subsequently make a correlation between the patient’s pressure needs and lattice samples stiffness.
Findings
A substantial and wide variation in lattice compressive behaviour was found depending on the key study variables. The proposed methodology made it possible to efficiently identify and adjust the pressure of the different areas of the product to adapt them to the elastic needs of the patient. In this sense, the characterization lattice samples turned out to provide an effective and flexible response to the pressure requirements.
Originality/value
This study provides a generalized foundation of lattice structural design and adjustable stiffness in application of pressure cushions, which can be equally applied to other designs with similar purposes. The relevance and contribution of this work lie in the proposed methodology for the design of personalized therapeutic products based on the use of individual lattice structures that function as independent customizable cells.
Keywords
Citation
de la Rosa, S., Mayuet, P.F., Silva, C.S., Sampaio, Á.M. and Rodríguez-Parada, L. (2024), "Design and characterization of 3D-printed TPU-based lattice structures. Application to methodology for the design of personalized therapeutic products", Rapid Prototyping Journal, Vol. 30 No. 11, pp. 72-86. https://doi.org/10.1108/RPJ-08-2023-0287
Publisher
:Emerald Publishing Limited
Copyright © 2024, Sergio de la Rosa, Pedro F. Mayuet, Cátia S. Silva, Álvaro M. Sampaio and Lucía Rodríguez-Parada.
License
Published by Emerald Publishing Limited. This article is published under the Creative Commons Attribution (CC BY 4.0) licence. Anyone may reproduce, distribute, translate and create derivative works of this article (for both commercial and non-commercial purposes), subject to full attribution to the original publication and authors. The full terms of this licence may be seen at http://creativecommons.org/licences/by/4.0/legalcode
1. Introduction
Additive manufacturing (AM) processes involve layered printing of materials, promoting a more active interaction between manufactured object’s properties and manufacturing variables (Afonso et al., 2021). In this sense, the possibility of manufacturing more complex geometries with a high capacity for customization, as well as, a significant reduction in manufacturing time and cost, is enhanced (Almesmari et al., 2023; Rahmatabadi et al., 2023b). AM processes have been evolved to meet the production appeal of complex structures with good resolution, being very useful when low production volumes and frequent design changes are required (Nazir et al., 2023; Rahmatabadi et al., 2023a). A variety of methods and materials have been developed over the years, transforming assembly processes and production. Rapid prototyping, medical equipment materials and high added value customized products, are some of the main goals in the evolving of AM processes (Ghomi et al., 2021; Jiménez et al., 2019; Lu et al., 2022; Rosa et al., 2021b; Wang et al., 2020a; Yang et al., 2022). Some of the main developed AM processes can be fused filament fabrication (FFF), stereolithography (SLA) or selective laser sintering (SLS). In general, each AM process shows advantages and disadvantages that give the final manufactured object totally different functional and aesthetics features. SLS is often used for its accuracy and suitability in working with elastomeric powders to create a complete durable object. However, SLS printing methods can be expensive and include post-processing demands. The SLA allows working with very small resolutions that are difficult to achieve with FFF and SLA resins are usually not comparable in strength and mechanical performance to other AM processes. By comparison, FFF is less expensive process, with low cost of manufacturing materials and simplicity compared to other AM processes, while offering objects with good resolution and mechanical performance. Resin-based systems could also eventually be a viable technique, although for now FFF production arguably represents the most cost-effective explanation for customizing products (Choudhari and Patil, 2016; Kafle et al., 2021; Srivastava and Gaur, 2020). This is reflected in the currently priority use of this technology in the design and development processes of medical equipment and orthotics (Aydin et al., 2019; Ma et al., 2019a; Sharma et al., 2020; Srivastava and Gaur, 2020). FFF process known as most common 3 D printing, mainly uses thermoplastic filaments (Chiocca et al., 2022; Jain and Gupta, 2022; Prajapati et al., 2022b; Rahmatabadi et al., 2023b). In this process, the rheology of the polymeric filament is an essential characteristic, allowing the filaments to be heated to a semi-liquid state during printing and solidify at room temperature to form the object (Karamimoghadam et al., 2023; Moradi et al., 2021). Design and manufacturing variables dependence on the physical and mechanical properties, as well as product customization are the main research challenges in recent years (Gao et al., 2019; Rahmatabadi et al., 2023b; Rodríguez-Parada et al., 2021; Tang et al., 2021; Wang et al., 2020b). The general AM processes compatibility with elastic materials, such as FFF process, has increased the use of elastomeric polymers in recent years (Abdulhameed et al., 2019; Herzberger et al., 2019). Thermoplastic elastomers (TPE), and especially, thermoplastic polyurethanes (TPU) have become a popular choice among different elastic materials (González-Henríquez et al., 2019; Harris et al., 2019; Xiao and Gao, 2017). Regarding resourcing to elastomeric materials suitable for AM technologies, literature reports that TPUs seem to be a good option for generating enough potential energy to restore original shape in rigid and elastic objects (Rahmatabadi et al., 2023b; Rodríguez-Parada et al., 2021). Also, TPU softness and biocompatibility turned out to be useful for research scopes such as orthopaedics and trauma medicine (Davia-Aracil et al., 2018; Tang et al., 2019; Xiao and Gao, 2017). TPU performance was shown to be proportional to infill density regardless of sample thickness, establishing the suitability of this material for deformation and energy absorption applications (Bates et al., 2016; Tsang et al., 2019). In addition, it was established that the TPU together with the geometric properties of the printed object, would allow to obtain specific properties in terms of texture, flexibility and other sensations (Almesmari et al., 2023; de la Rosa et al., 2023; Ma et al., 2019; Tsang et al., 2019), that would allow adjusting the elasticity in the development of all kinds of TPU-based applications and products that require a specific elasticity (Rosa et al., 2021a; Tafazoli and Nouri, 2022). Therefore, the study of the functional properties related to the elasticity provided by the infill material and geometrical features is especially relevant (Lee et al., 2019; Rodríguez-Parada et al., 2021). In this sense, conventional manufacturing methods currently do not rival FFF processes because it is possible to generate free-support non-solid internal geometries with the possibility of providing a different elasticity to the same product, as well as obtaining elastic materials from rigid materials and different elasticities from the same elastic material (Herzberger et al., 2019; Rahmatabadi et al., 2023b; Rodríguez-Parada et al., 2021). As a consequence, the versatility and control over the manufacturing process offered by AM, has led to a growing trend in the use of lattice structures, making available a wide range of possibilities in the manufacture of lattice geometries and structures with more complex architectures (Almesmari et al., 2023; Günaydın et al., 2022; Kumar et al., 2020; de la Rosa et al., 2023; Nazir et al., 2023; Niknam and Akbarzadeh, 2020a; Prajapati et al., 2022a; de la Rosa et al., 2021). Several geometric lattice structures have been tested to improve their performance as a function of their mechanical properties (Almesmari et al., 2023; Günaydın et al., 2022; Mahbod and Asgari, 2019; Momeni et al., 2019; Nazir et al., 2023; Niknam and Akbarzadeh, 2020; Pham et al., 2019; Prajapati et al., 2022a; Sha et al., 2018; Wang et al., 2022). It was found that geometric and manufacturing variables, as well as the elastic variant, play a critical role in the variation of stiffness, deformation mechanisms and energy absorption properties (Bates et al., 2019; Dar et al., 2020; Habib et al., 2019; de la Rosa et al., 2021; Tafazoli and Nouri, 2022), even an adequate hybridization of several structures can lead to reducing the universal anisotropy (Khaleghi et al., 2021). Several TPU-based lattice samples and materials were designed and tested to be applied in personalized product design, showing that lattice samples with different cell topologies could obtain an increase in stiffness for the same manufacturing conditions, assuming an improvement in the efficiency of the production of lattice samples (De La Rosa et al., 2021). Consequently, the development of elastic behaviour profiles applied to the design of products with elastic properties adapted to previously specified energy ranges has been made possible (De La Rosa et al., 2021; de la Rosa et al., 2023; Maskery et al., 2017; Prajapati et al., 2022a). This idea turned out to be highly compatible with research interests in sectors related to medicine such as trauma medicine (Lu et al., 2022; de la Rosa et al., 2021), where products with elastic properties specifically focused on the needs of the patient are used to guarantee the comfort (Lopes et al., 2019; Martins et al., 2014). The development of design methodologies and innovative solutions to guarantee the quality of products taking into account personalization and the degree of adaptation, are some of the main goals in the design of personalized products (Barrios-Muriel et al., 2020; Cantaboni et al., 2022; Kumar and Chhabra, 2022; Lu et al., 2022; Orozco et al., 2019). For example, de la Rosa et al. used compression data of simulated TPU lattice samples as a methodology to predict the behaviour of untested lattice samples. The results were validated by carrying out a case study based on the personalized design of a therapeutic ball. The possibility of using statistical data such as contour plots to predict which geometric and manufacturing variables are necessary for lattice samples to exhibit specific elastic behaviour was demonstrated. Each of the results obtained showed that the studied variables were within the intervals predicted by the contour plots, even for previously considered values of unstudied parameters (de la Rosa et al., 2023). In this sense, designs with adjustable module have become necessary for applications in therapeutic products since the contact tension between body parts and the environment is a critical factor for the development of problems such as ulcers. Davia-Aracil et al. presented a CAD methodology to design and manufacture therapeutic insoles by Additive Extrusion technologies using extruded 2 D projected structures. This methodology was verified both practically and economically by several prototypes, demonstrating that the production of anatomical insoles using AM is actually cost-effective and feasible at an industrial level (Davia-Aracil et al., 2018). Studies of porous structural units in terms of geometric variables and their correlation with mechanical properties have been developed. Mathematical relationships methods between the effective performance and geometric variables were derived and subsequently used in the construction of porous structural design for adjustable gradient porous diabetic insoles applications. Pressure maps of users' footsteps were taken as a reference to corroborate that porous structures could reduce pressure peaks in comparison with conventional insoles (Ma et al., 2019; Tang et al., 2019; Wang et al., 2017). García-Dominguez et al. presented a design methodology for the optimization of AM parts and explored the synergies between AM, parametric design and optimization processes. A topologically optimized heel geometry has been designed through infill and shell optimization, adapting it to local forces in a non-continuous way throughout the heel. The methodology generates as a result a continuous cellular structure that extends along the optimized geometry of the part which is composed of an open cellular infill structure and a wireframe shell. For this, a gait analysis is carried out to determine the support points of the foot (García-Dominguez et al., 2020a, 2020b). Other examples focused in the development of orthoses and products for the localized treatment of different parts of the body have been developed (Barrios-Muriel et al., 2020; de Carvalho Filho et al., 2020; Haro et al., 2018; Orozco et al., 2019; Santos et al., 2017; Yan et al., 2019). In general, the method of 3D scanning of the user’s body parts is observed to build a product from the scanned surfaces using CAD and topological optimization.
In conclusion, it is seen that many studies have provided feasible methods in the field of personalized therapeutic products, few of them focus on porous structural units (size, geometric parameter, porosity and effective modulus) in order of stress distribution optimization in human parts and traditional products through the compressive properties of elastic materials. It is notable that most of the research and proposed methodologies are consistent with the foot area. It has been shown that general research focuses on the design of continuous geometry products, without taking into account possible changes in the shape of the product caused by comfort problems derived from the patient’s adaptation period (Brienza et al., 2010; Lee et al., 2016). Due to the mentioned lack of similar outcomes in the specialized literature, this paper is likely to fill the gap in the state-of-the-art problems and supply relevant data. One of the problems to be addressed in this paper is the consideration of products with non-continuous geometry that allows the variation of the parts of the product without the need to interact or modify related parts or manufacture a new product in its entirety. Likewise, the design of personalized products focused on other parts of the body beyond the foot area is considered.
For all the above-described reasons, the main objective of this paper focuses in the study on the lattice structures in terms of the geometrical variables, manufacturing variables and material-based and their correlation with compressive behaviour for their application in a methodology for the design and development of personalized elastic therapeutic products (Figure 1). Some of the main goals of the proposed methodology is to identify the most relevant areas of the product to adapt the elastic properties of these identified areas to the specific needs required by the patients. Specifically, the aim is to use a parametric design that can adapt the elastic properties of lattice structures with respect to specific patient data obtained by means of reverse engineering. For the study, existing products on the market are taken as a reference for the analysis of their functional operation. This work advances the current state of knowledge in the area of personalized elastic products in terms of providing a generalized foundation of lattice structural design and adjustable stiffness in the application of a case study based on the design of a pressure cushion, which can be equally applied to other designs with similar purposes.
2. Materials and methods
2.1 Design of supportless lattice structures
The supportless lattice structures are based on the design for AM principles. Several critical features such as overhang angle and bridging distance are considered in the design of a support-free lattice structure. Overhang is related to the maximum angle up to which a 3D parts can be 3D printed support free with, where a maximum overhang angle of 45° is considered a safe approximation. Moreover, the bridging distance depends on the melt viscosity of the extruded material and its cooling rate (Prajapati et al., 2022a). Both features can be optimized by adjusting variables such as printing speed, printing temperature and cooling speed among others. Therefore, based on the above approaches, the supportless Schwarz closed-cell topology was used for the samples’ latticing process based on its good compression behaviour and its feasibility to be support-free printed by using FFF technologies. According to Prajapati et al. (2022a), the unit cell has been designed for this work considering the overhang angle and bridging distance (Figure 2).
Several samples design have been studied. The samples were designed through generative design and architected materials modules in Ntopology® engineering design software. The established dimensions for samples were 45 mm × 45 mm ×45 mm (Figure 3). In addition, several geometric variables such as unit cell size and unit cell thickness, as well as manufacturing variables such as layer height were studied. Specifically, unit cell size varied according to the values 11.5 mm, 15 mm and 22.5 mm, unit cell thickness varied according to the values 0.4 mm and 0.6 mm and layer height varied according to the values 0.1 mm and 0.2 mm (Figure 2). In this sense, a total of 12 different samples were designed.
2.2 Materials
The materials used in this study were a 92 A Shore Hardness recycled TPU (Reciflex TPU), an 82 A Shore Hardness standard TPE (Filaflex) and a 95 A Shore Hardness standard TPU (Filaflex). Each material was chosen to characterize the influence of material nature and Shore hardness. Specifically, all the materials were purchased from the manufacturer Recreus 3 D, where the main properties given by the manufacturer are detailed in Table 1.
2.3 Support-free additive manufacturing of lattice samples
Each material was used to manufacture each designed sample, resulting in a total of 36 manufactured samples. The variables selected for the manufacture of the samples are in accordance with the manufacturer’s recommendations and previous tests. The variables used are detailed in Table 2.
The production of the samples was made in the Creality® CR-5 FFF printer using a 0.4 mm extrusion nozzle (Figure 4), according to Ma et al. (2019). Moreover, according to Popescu et al. (2018), the specimens have been printed one by one to avoid the tensions in the models that could be generated by a simultaneous manufacturing process.
2.4 Procedure of evaluation
As mentioned before, a total of 36 test samples have been tested. The compression tests were carried out on the Shimadzu Autograph model AG-X series machine, with a maximum applicable axial force of 50 kN and a displacement resolution of 0.0208 µm. All test variables were managed with the help of the universal software Trapezium®AG-X series for Windows®. According to ISO, 2003, the compression tests were performed at a constant speed, where speed was set at 1 mm/min. The loading direction was kept at 0° to the print direction to assess the compressive strength of the lattice samples to avoid possible variations in stiffness in different directions depending on the deformation mode that governs in that direction (Khaleghi et al., 2021). The lower plate was set to fixed while the upper plate moved up to approximately 70% compression of the lattice samples (Figure 5). The results obtained in terms of compressive strength through the stress–strain engineering curves were analysed, and the elastic modulus of the different samples tested was evaluated to quantify the elasticity and efficiency according to the study variables, in accordance with (ISO, 2003).
From the compression tests data, Stress “σ” was obtained according to Equation (1):
The Young’s modulus (E) indicates the relationship between the increase in stress and the increase in the unit longitudinal deformation that occurs during compression of the samples, and was obtained from its equivalence with the slope of the initial elastic region of the stress–strain curve by means of the following equation (2) (Belingardi et al., 2001; Duan et al., 2019; Habib et al., 2018):
From stress–strain data set, a statistical treatment was carried out with the Minitab® software for the generation of graphs to analyse from a clearer perspective the influence of each parameter and material on the compression behaviour of elastic lattice structures.
2.5 Experimental validation: case study on the design of a pressure cushion adapted to the patient
2.5.1 Aim and scopes
In the design of personalized elastic products in medical areas such as trauma medicine, one of the main problems to be addressed is always the adaptation of the product to the needs of patients to improve their comfort. To understand this problem, pressure cushions are taken as a reference. Pressure cushions are focused on people who spend a large number of hours a day sitting in the same position. The most widespread operation method is based on cells filled with air bags. The cells are distributed according to the main parts of the body, specifically the glutes and the biceps femoris area. Depending on the number of air bags contained in each cell of the cushion, it is possible to modify the general compression mode to distributing the body pressure points in the most critical areas. For the present case study, a Vicair® cushion model was considered as a reference. As previously mentioned, this model makes use of air bags that allow the compression capacity of the different cushion cells to be modified (Figure 6).
The initial stages of adaptation of the patient to the product can take weeks, months or even persist over time due to health problems derived from the continuous friction of the patient’s body with the product. Due to this, currently pressure cushions already have independent cells to be able to act specifically on parts of the product without the need to interact or modify the rest of its parts (Wheelchair, 2024). This fact justifies the focus of the proposed design methodology on the division of elastic areas. On the other hand, modifying the compression modes of the cushion by adding or removing air bags can be very tedious, especially in the initial phases when the patient demands more changes due to the adaptation process to the product. In this sense, the focus of the proposed design methodology on the use of individual structures as independent cells is justified, to eliminate the need to deal with numerous airbags, making the customization of the compression mode of the cushion much more effective and efficient. The proposed case study aims to maintain the contact surface of the cushion in a similar way to the current method. As mentioned above, the micro-bags are grouped into different woven and bonded cells that form the cushion. In this case, the application method involves replacing the air bags with individual parameterized lattice samples located in individual woven and bonded cells to mostly avoid possible problems generated by individual lattice samples and the resulting discontinuities. This operation method allows the performance of each cell to be quantified through samples stiffness.
Therefore, the main objective of this methodology is to identify the most relevant parts in products to create a correlation between the patient’s needs and the compressive features of lattice samples. The proposed conceptual procedure (Figure 7) is based on correlating the patient’s pressure data with the stiffness data of lattice samples, as a way of translating the pressure needs into characterized geometrical and manufacturing variables of said samples.
Unlike the previously mentioned currently existing methodologies in the state of the art, the contribution and novelty of the proposed methodology relies on the use of individual lattice samples. This fact is justified from the perspective of allowing each area of the product to be adjusted independently, either by replacing some of the individual structures or by exchanging the position of those already contained in the product. In this sense, when the patient needs a change due to lack of comfort, the lattice samples can be exchanged internally within the cushion itself or even reuse these structures for other patients. Therefore, it is not necessary to make exhaustive changes to the entire product, optimizing the use of resources that would otherwise be difficult to carry out in other methodologies proposed in other current methods.
2.5.2 Pressure data measurement
Seat pressure data have been calculated using a Teximat pressure blanket, from the manufacturer Vermeiren. The total surface of the blanket equates dimensions of 600 × 600 mm, covered with flexible and adaptable fabric, with a sensitive area of 450 × 450 mm that contains a total of 1024 pressure sensors (Figure 8) (Texis, 2024). Several measurements are made until finding the optimal seating position. In parallel, the pressure blanket is connected via USB 2.0 connectivity to the Teximonitor® software to transcript the signals sent by each of the pressure sensors enabling to extract a list in .csv format of the pressure data for each of the pressure sensors, as well as a graphic pressure map in .pdf format.
2.5.3 Pressure data analysis
Each patient may have specific pressure needs derived from their body shape or health problems. Therefore, the proposed procedure consists of dividing pressure map in different zones according to pressure values and action priority. This enables to consider the pressure needs for each area independently, by using equation (4):
Unlike the previously mentioned methodologies currently existing in the state of the art, the proposed methodology not only has the objective of being able to analyse pressures to reduce pressure points that may cause discomfort to the patient. The correction factor offers complete freedom in establishing which areas will accumulate more or less tension enabling to customize solutions to improve comfort and giving trauma medicine professionals complete freedom to achieve other related objectives, such as, correcting sitting postures.
2.5.4 Design parameterization
To correlate Pcr values with the stiffness of the tested lattice samples for the different areas in the pressure map, a relationship with macro functions is made between the mean Pcr of the areas and the stiffness value provided by tested elastic lattice samples. Because the pressure blanket has 1,024 sensors, associating a lattice sample to each sensor value would mean manufacturing 1,024 lattice samples, which would entail a very high cost of material and manufacturing time. To avoid this, groupings of values from nine neighbouring sensors are made to make the equivalence to the stiffness value of each sample (Figure 9).
3. Results and discussion
This section shows the results in terms of the influence of geometric and manufacturing variables, as well as elastic material variants used, on the behaviour of elastic lattice structures for their application in personalized elastic product design.
3.1 Sample characterization
Stiffness values of each of the samples were obtained from the range of stresses recorded from 5% and 10% of compression displacement in the elastic region of stress–strain curves (Table 3).
In the interval plot (Figure 10), the upper interval limit represented the values associated with the 0.1 mm layer height and the lower interval limit represented the values associated with the 0.2 mm layer height. The interval plot shows a strong correlation between the values of Young’s modulus and Shore A hardness. The samples based on TPU 95A presented higher stiffness values compared to the samples based on TPE 82A. The study variables caused changes sufficiently significant effects on the elasticity of the network samples, giving rise to a wide range of stiffness values to satisfy a wide range of elastic needs. In this sense, the Schwarz topology was shown to support a wide range of stiffness values, which could derive from the ability of this type of cells to have more modules in a wide range of volume fractions than other types of cells (Khaleghi et al., 2021).
An increase trend in Young’s modulus values for smaller unit cell size have been detected, especially when unit cell size decreases from 15 mm to 11.5 mm, which may be derived from the notorious decrease in the number of cells and samples density (De La Rosa et al., 2021). In this sense, a response relationship between the variables is shown. The variation in sample stiffness produced when unit cell size increased from 11.5 mm to 22.5 mm is clearly influenced by unit cell thickness and layer height. As an example, it has been detected that Young’s modulus values decreased by approximately 78% in TPU 95A-based samples with unit cell thickness 0.4 mm and layer height 0.1 mm, and 84% in samples with unit cell thickness 0.6 mm. In the same way, it has been detected that Young’s modulus values decreased by approximately 75% in TPE 82A-based samples with unit cell thickness 0.6 mm and layer height 0.1 mm, and 70% for samples with layer height 0.2 mm. Consequently, the variation in Young’s modulus produced by unit cell size proved to be more noticeable for higher unit cell thickness and lower layer height values. Related to unit cell thickness variable, it has been found that the variation in Young's modulus values produced by unit cell thickness is more noticeable in samples with a layer height 0.1 mm in comparison with samples with a layer height 0.2 mm when unit cell thickness increased from 0.4 mm to 0.6 mm. This phenomenon may be related to the decrease in stiffness derived from the reduction in the number of printing layers when using a higher layer height. In addition, the percentages reflected variations according to the Shore A hardness variable. Results demonstrated that Young’s modulus values increased by approximately 71% for TPE 82A-based samples with a layer height 0.1 mm and 57% for a layer height 0.2 mm. Similarly, Reciflex-based samples presented decrease percentage of 75% for samples with a layer height 0.1 mm and 65% for a layer height 0.2 mm, and TPU 95A-based samples presented 45% for samples with a layer height 0.1 mm and 42% for samples with a layer height 0.2 mm. In the same way, related to layer height variable, the variation in Young’s modulus produced by the layer height was found to be more noticeably in samples with unit cell thickness 0.6 mm when layer height increased from 0.1 mm to 0.2 mm. This phenomenon may be related to the intrinsic increase in the sample density produced by the increase in unit cell thickness (Rodríguez-Parada et al., 2021). Reciflex-based samples presented 14% for samples with unit cell thickness 0.4 mm and 34% for Unit cell thickness 0.6 mm. Similarly, Young’s modulus values decreased by approximately 11% for TPE 82A-based samples with unit cell thickness 0.4 mm and 50% for a unit cell thickness 0.6 mm, and TPU 95A-based samples presented 31% for samples with unit cell thickness 0.4 mm and 34% for samples with unit cell thickness 0.6 mm. Analysing the variation of stiffness in the data presented, it is concluded that the variation of the percentages between samples under changes in unit cell thickness and layer height is more noticeably for materials with lower Shore A hardness, with TPU 95A being the material that presents the least variation between the percentages obtained. This could be justified from the elasticity of the materials, where materials of lower hardness would allow more extensive and noticeably variations in sample stiffness. Therefore, it is concluded that in applications that require stiffness adjustments depending on unit cell thickness variations, or applications where the surface finish is not important, it is preferable to use materials with a lower Shore A hardness, since the variation in the stiffness of the samples derived from the variation in the height of the layer or thickness is more noticeable.
Finally, it was detected that the same stiffness can be achieved using different variables. As an example, Reciflex-based samples with unit cell size 22.5 mm, unit cell thickness 0.6 mm and layer height 0.2 mm have similar stiffness in comparison with and TPU 95A-based samples with unit cell size 22.5 mm, unit cell thickness 0.6 mm and layer height 0.1 mm. In this sense, the layer height allows the sample manufacturing time to be considerably reduced and at the same time reduce the environmental impact by using a recycled material. This phenomenon is reflected in the same way for other sets of samples where adjustments can be made to obtain similar stiffness and optimised manufacturing process at the same time. So from the perspective of product design, this can be a great advantage for the design of more sustainable products with the use of recycled materials, the reduction of material waste and manufacturing time.
3.2 Design of a personalized pressure cushion adapted to the patient
The elastic needs of the patient’s seat have been measured and analysed according to the procedure previously described. Analysing the pressure map obtained from pressure data measurement (Figure 11), it is observed that the maximum Ps is 2.7 N/cm2. The pressure map obtained is the visual representation of the raw data collected by the sensors during the measurement process with the patient. An equivalence of the data has been made to the international system of units and Ps values have been graphically associated with the pressure map obtained. Also, laterality was found to be 58% and 42% on the left and right section, respectively, obtaining the highest Ps values in the left section of the pressure map. It is observed that, in both sections, the areas with the highest Ps values are represented in the gluteal area. On the other hand, there is a continuous distribution of stresses up to the extremes of the pressure map where there are peripheral areas whose Ps is very small.
The laterality data provided by the case study is interesting from the perspective of product design. Therefore, as an example for this case study, the requirements considered are to reduce laterality and release tensions by 10% in the areas of maximum pressure (green, orange and red areas).
According to requirements described above, different elastic areas have been identified in the pressure map (Figure 12). It should be noted that the maximum Ps value in the left section is 3.05 MPa compared to 2.50 MPa in the right section. Therefore, to reduce laterality, it was defined that a Fcr of 20% (Fcr = 0.8) should be applied to the area of maximum Ps of the left section to equalize the right section. On the other hand, in the areas of maximum Ps in both sections, it is determined that it is necessary to apply an additional Fcr of 10% to release pressures. The proposed requirements and identified elastic areas are exemplary and could be modified in a personalized way for each patient if indicated by professionals in the sector.
The proposed Fcr are applied to the Ps values using equation 4. In this sense, considering the average of the Pcr values of the neighbouring sensors and the size of the pressure sensors (14 mm), it is obtained a total of 100 Pcr values. Averaging of the values of neighbouring sensors is carried out so that the values of Pcr is associated in an orderly manner with each of the elastic zones of the pressure map, to make the equivalence with the stiffness of the characterized lattice samples (Figure 13).
Finally, a macro association has been made between Pcr values and the stiffness values collected from the characterized elastic lattice samples. Then, in the personalized pressure cushion design, for each Pcr value, the closest stiffness value provided by the characterized elastic lattice structures is associated (Figure 14). For a detailed correlation for the final application of the product, the characterization of the stiffness of the elastic samples is used together with the design variables (Table 3). In this way, it has been possible to parameterize the elastic needs, translating into the design and manufacturing variables, as well as elastic material variant so that the lattice sample offers the necessary stiffness. It is noticeable that Area 3 presents the greatest accumulation of tensions. Therefore, when performing the correlation, it is expected that lattice samples of greater rigidity will be necessary. In this sense, when analysing the assignment of variables after adjusting the pressures to the requirements, it can be observed that in the white areas corresponding to Area 3, structures with greater rigidity related to materials with greater Shore A hardness are recommended, with lower values of unit cell size, larger cell thickness and higher layer height values. The correlation occurs with equal effectiveness for the rest of the areas with their specific requirements. Therefore, an effective correlation between the elastic needs and the parameterization of the network samples has been achieved. This selection of variables validates all the conclusions obtained in this work on the elastic behaviour of reticular samples, corroborating the effectiveness and application of the results obtained in this paper.
4. Conclusions
In this paper, a new design method was proposed for the design of personalized elastic therapeutic products based on the study on the TPU-based lattice samples in terms of the geometrical variables, manufacturing variables and material-based variants and their correlation with compressive behaviour. Experimental results demonstrated that the study variables caused sufficiently significant changes in the elasticity of the lattice samples, giving rise to a wide range of stiffness values to meet a wide range of elastic needs. A significant response relationship was found between the variables studied. Specifically, significant increases in stiffness were found to be strongly correlated with higher unit cell size and layer height values, and smaller unit cell thickness values, respectively. Regarding the Shore A hardness variable, the percentages of variation in stiffness between samples due to changes in variables tend to be more noticeable for materials with lower Shore A hardness. In addition, it was found that the same stiffness can be achieved in different sets of samples using different manufacturing configurations enabling the reduction in environmental impact through the use of recycled materials and optimized manufacturing processes with less material and manufacturing time consumption.
The case study provided and verified a generalized foundation of lattice structural design and adjustable stiffness in application of pressure cushions, which can be equally applied to other designs and products with similar purposes, as well as, the integration as software in the design process. The proposed methodology differed from other methodologies existing in the state of the art, since it considers the use of individual lattice structures that function as independent cells of a pressure cushion, with the objective of providing the product design with freedom to redesign and modify each one of the identified elastic areas without the need to interact with the rest of the areas and lattice structures. The characterization of lattice samples in function of study variables turned out to be effective in providing a rapid and flexible response to the elastic requirements. The division of elastic areas proved to be favourable since the correction factor established in each zone allowed the stiffness of the lattice samples to be correctly correlated to the elastic requirements established in the case study. In this sense, one of the most common problems related to the design changes requested by the patient’s adaptation process to the product over time or the entire useful life of the product was solved. Furthermore, the proposed methodology allowed optimizing the use of resources that would otherwise be difficult to carry out in other methodologies proposed in the current state of the art, since the lattice structures allow them to be exchanged within the same product for behaviour modification, or they could be reused for other patients with similar needs. The quality of life of patients could be benefited with the proposed method from the perspective of providing designers and professionals in the sector with the ability to quantify patient pressure data in design and manufacturing variables with the aim of adjusting with total freedom these variables according to the pressure needs. This would avoid trial and error clinical trials to adjust the cushion to the patient's needs, reducing the work time of the professional team and, therefore, indirectly improving patient quality by reducing visit times in clinical trials. Compared to other methods, the proposed methodology was not limited to optimizing the distribution of stresses, enabling its use in other applications, such as, modification or correction of sitting postures since the individual lattice samples allow a high degree of customization in the differentiated areas.
As a future line of work, it is proposed to address the possible limitations related to the assembly of separate structures and the resulting discontinuities. It is proposed to study how to improve the continuity of the design without losing the properties related to the use of lattice samples as independent cells, and challenges related to other applications with non-vertical compression loading of lattice samples. For another part, the way in which the methodology is described is designed from the point of view of its integration as software in the design process. Therefore, an attempt at software integration of the methodology is proposed for its effective application and generalizability.
Figures
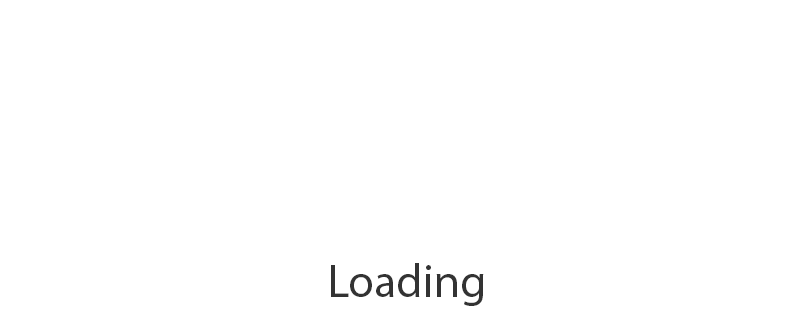
Figure 6
Reference pressure cushion (Wheelchair, 2024)
Main materials properties
Material | Filament diameter (mm) | Density (g/cm3) | Tensile strength (MPa) | Printing temperature (°C) | Shore a Hardness |
---|---|---|---|---|---|
TPE 82 A | 1.75 | 1.17 | 43 | 215 – 250 | 82 A |
Reciflex | 1.75 | 1.22 | 45 | 220 – 235 | 92 A |
TPU 95 A | 1.75 | 1.08 | 55 | 215 – 250 | 95 A |
Source: Table by authors
Main manufacturing variables
Variables | Value |
---|---|
Layer height (mm) | 0.2 |
Layer width (mm) | 0.4 |
Printing temperature (°C) | 220 |
Bed temperature (°C) | 35 |
Printing speed (mm/s) | 20 |
Displacement speed (mm/s) | 180 |
Retraction | Enabled |
Retraction distance (mm) | 3.5 |
Retraction speed (mm/s) | 40 |
Source: Table by authors
Sample’s stiffness data
Young’s modulus (MPa) | |||||
---|---|---|---|---|---|
Unit cell size (mm) | Unit cell thickness (mm) | Layer height (mm) | TPE 82 A | RECIFLEX | TPU 95 A |
11.5 | 0.4 | 0.1 | 0.45 | 0.67 | 1.42 |
0.2 | 0.38 | 0.52 | 1.14 | ||
0.6 | 0.1 | 1.52 | 2.13 | 2.92 | |
0.2 | 0.78 | 1.45 | 2.33 | ||
15 | 0.4 | 0.1 | 0.22 | 0.40 | 0.89 |
0.2 | 0.21 | 0.38 | 0.58 | ||
0.6 | 0.1 | 0.71 | 1.49 | 1.71 | |
0.2 | 0.44 | 0.95 | 1.03 | ||
22.5 | 0.4 | 0.1 | 0.10 | 0.11 | 0.32 |
0.2 | 0.08 | 0.13 | 0.19 | ||
0.6 | 0.1 | 0.38 | 0.75 | 0.47 | |
0.2 | 0.23 | 0.47 | 0.27 |
Source: Table by authors
References
Abdulhameed, O., Al-Ahmari, A., Ameen, W. and Mian, S.H. (2019), “Additive manufacturing: challenges, trends, and applications”, Advances in Mechanical Engineering, Vol. 11 No. 2, pp. 1-27, doi: 10.1177/1687814018822880.
Afonso, J.A., Alves, J.L., Caldas, G., Gouveia, B.P., Santana, L. and Belinha, J. (2021), “Influence of 3D printing process parameters on the mechanical properties and mass of PLA parts and predictive models”, Rapid Prototyping Journal, Vol. 27 No. 3, pp. 487-495, doi: 10.1108/RPJ-03-2020-0043/FULL/PDF.
Almesmari, A., Sheikh-Ahmad, J., Jarrar, F. and Bojanampati, S. (2023), “Optimizing the specific mechanical properties of lattice structures fabricated by material extrusion additive manufacturing”, Journal of Materials Research and Technology, Vol. 22, pp. 1821-1838, doi: 10.1016/J.JMRT.2022.12.024.
Aydin, L., Kucuk, S., Cetinarslan, B., Canturk, Z., Peker, A., Ege, M., Yalcin, F. and Ege, G.K. (2019), “Development and biomechanical validation of medical insoles to prevent foot ulcers on diabetic patients by means of thermoplastic elastomers and additive manufacturing technologies”, 2019 Medical Technologies Congress (TIPTEKNO), doi: 10.1109/TIPTEKNO.2019.8895086.
Barrios-Muriel, J., Romero-Sánchez, F., Alonso-Sánchez, F.J. and Salgado, D.R. (2020), “Advances in orthotic and prosthetic manufacturing: a technology review”, Materials, Vol. 13 No. 2, p. 295, doi: 10.3390/ma13020295.
Bates, S.R.G., Farrow, I.R. and Trask, R.S. (2016), “3D printed polyurethane honeycombs for repeated tailored energy absorption”, Materials & Design, Vol. 112, pp. 172-183, doi: 10.1016/j.matdes.2016.08.062.
Bates, S.R.G., Farrow, I.R. and Trask, R.S.S. (2019), “Compressive behaviour of 3D printed thermoplastic polyurethane honeycombs with graded densities”, Materials & Design, Vol. 162, pp. 130-142, doi: 10.1016/j.matdes.2018.11.019.
Belingardi, G., Montanini, R. and Avalle, M. (2001), “Characterization of polymeric structural foams under compressive impact loading by means of energy-absorption diagram”, International Journal of Impact Engineering, Vol. 25 No. 5, pp. 455-472.
Brienza, D., Kelsey, S., Karg, P., Allegretti, A., Olson, M., Schmeler, M., Zanca, J., Geyer, M.J., Kusturiss, M. and Holm, M. (2010), “A randomized clinical trial on preventing pressure ulcers with wheelchair seat cushions”, Journal of the American Geriatrics Society, Vol. 58 No. 12, p. 2308, doi: 10.1111/J.1532-5415.2010.03168.X.
Cantaboni, F., Ginestra, P., Tocci, M., Colpani, A., Avanzini, A., Pola, A. and Ceretti, E. (2022), “Modelling and FE simulation of 3D printed Co-Cr lattice structures for biomedical applications”, Procedia CIRP, Elsevier, Vol. 110 No. C, pp. 372-377, doi: 10.1016/J.PROCIR.2022.06.066.
Chiocca, A., Tamburrino, F., Frendo, F. and Paoli, A. (2022), “Effects of coating on the fatigue endurance of FDM lattice structures”, Procedia Structural Integrity, Vol. 42, pp. 799-805, doi: 10.1016/J.PROSTR.2022.12.101.
Choudhari, C.M. and Patil, V.D. (2016), “Product development and its comparative analysis by SLA, SLS and FDM rapid prototyping processes”, IOP Conference Series: Materials Science and Engineering, Vol. 149 No. 1, pp. 1-8, doi: 10.1088/1757-899X/149/1/012009.
Dar, U.A., Mian, H.H., Abid, M., Topa, A., Sheikh, M.Z. and Bilal, M. (2020), “Experimental and numerical investigation of compressive behavior of lattice structures manufactured through projection micro stereolithography”, Materials Today Communications, Vol. 25, pp. 1-12, doi: 10.1016/J.MTCOMM.2020.101563.
Davia-Aracil, M., Hinojo-Pérez, J.J., Jimeno-Morenilla, A. and Mora-Mora, H. (2018), “3D printing of functional anatomical insoles”, Computers in Industry, Vol. 95, pp. 38-53, doi: 10.1016/J.COMPIND.2017.12.001.
de Carvalho Filho, I.F.P., Medola, F.O., Sandnes, F.E. and Paschoarelli, L.C. (2020), “Manufacturing technology in rehabilitation practice: Implications for its implementation in assistive technology production”, Advances in Intelligent Systems and Computing, Vol. 975, pp. 328-336, doi: 10.1007/978-3-030-20216-3_31/COVER.
de la Rosa, S., Mayuet, P.F., Pardo-Vicente, M.A. and Rodríguez-Parada, L. (2023), “Influence of TPU lattice structures on functional properties for the design of customized rehabilitation products”, Lecture Notes in Mechanical Engineering, pp. 914-924, doi: 10.1007/978-3-031-15928-2_80/COVER.
De La Rosa, S., Mayuet, P.F., Ramón, J., Salgueiro, M. and Rodríguez-Parada, L. (2021), “Design of customized TPU lattice structures for additive manufacturing: influence on the functional properties in elastic products”, Polymers, Multidisciplinary Digital Publishing Institute, Vol. 13 No. 24, p. 4341, doi: 10.3390/POLYM13244341.
Duan, Y., Du, B., Shi, X., Hou, B. and Li, Y. (2019), “Quasi-static and dynamic compressive properties and deformation mechanisms of 3D printed polymeric cellular structures with kelvin cells”, International Journal of Impact Engineering, Vol. 132, pp. 1-16, doi: 10.1016/J.IJIMPENG.2019.05.017.
Gao, J., Luo, Z., Li, H. and Gao, L. (2019), “Topology optimization for multiscale design of porous composites with multi-domain microstructures”, Computer Methods in Applied Mechanics and Engineering, Vol. 344, pp. 451-476, doi: 10.1016/j.cma.2018.10.017.
García-Dominguez, A., Claver, J. and Sebastián, M.A. (2020a), “Integration of additive manufacturing, parametric design, and optimization of parts obtained by fused deposition modeling (FDM). A methodological approach”, Polymers, Vol. 12 No. 9, p. 1993, doi: 10.3390/POLYM12091993.
García-Dominguez, A., Claver, J. and Sebastián, M.A. (2020b), “Optimization methodology for additive manufacturing of customized parts by fused deposition modeling FDM. Application to a shoe heel”, Polymers, Vol. 12 No. 9, p. 2119, doi: 10.3390/POLYM12092119.
Ghomi, E.R., Khosravi, F., Neisiany, R.E., Singh, S. and Ramakrishna, S. (2021), “Future of additive manufacturing in healthcare”, Current Opinion in Biomedical Engineering, Vol. 17, p. 100255, doi: 10.1016/j.cobme.2020.100255.
González-Henríquez, C.M., Sarabia-Vallejos, M.A. and Rodriguez-Hernandez, J. (2019), “Polymers for additive manufacturing and 4D-printing: materials, methodologies, and biomedical applications”, Progress in Polymer Science, Vol. 94, pp. 57-116, doi: 10.1016/j.progpolymsci.2019.03.001.
Günaydın, K., Rea, C. and Kazancı, Z. (2022), “Energy absorption enhancement of additively manufactured hexagonal and re-entrant (auxetic) lattice structures by using multi-material reinforcements”, Additive Manufacturing, Vol. 59, p. 103076, doi: 10.1016/J.ADDMA.2022.103076.
Habib, F., Iovenitti, P., Masood, S. and Nikzad, M. (2018), “Fabrication of polymeric lattice structures for optimum energy absorption using multi jet fusion technology”, Materials & Design, Vol. 155, pp. 86-98, doi: 10.1016/j.matdes.2018.05.059.
Habib, F., Iovenitti, P., Masood, S., Nikzad, M. and Ruan, D. (2019), “Design and evaluation of 3D printed polymeric cellular materials for dynamic energy absorption”, The International Journal of Advanced Manufacturing Technology, Vol. 103 Nos 5/8, pp. 2347-2361, doi: 10.1007/s00170-019-03541-4.
Haro, F.B., Lopez-Silva, J., Pedro, P.S., Juanes, J.A., Pedro, A.B.S. and D’Amato, R. (2018), “Design and prototyping by additive manufacturing of a functional splint for rehabilitation of achilles tendon intrasubstance rupture”, ACM International Conference Proceeding Series, pp. 433-439, doi: 10.1145/3284179.3284253.
Harris, C.G., Jursik, N.J.S., Rochefort, W.E. and Walker, T.W. (2019), “Additive manufacturing with soft TPU – adhesion strength in multimaterial flexible joints”, Frontiers in Mechanical Engineering, Vol. 5, pp. 1-6, doi: 10.3389/fmech.2019.00037.
Herzberger, J., Sirrine, J.M., Williams, C.B. and Long, T.E. (2019), “Polymer design for 3D printing elastomers: recent advances in structure, properties, and printing”, Progress in Polymer Science, Pergamon, Vol. 97, p. 101144, doi: 10.1016/J.PROGPOLYMSCI.2019.101144.
ISO (2003), “ISO 604:2003 plastics – determination of compressive properties”, available at: www.iso.org/standard/31261.html (accessed 12 November 2023).
Jain, R. and Gupta, N. (2022), “Design optimization of PLA lattice in 3D printing”, Materials Today: Proceedings, Vol. 59, pp. 1577-1583, doi: 10.1016/J.MATPR.2022.02.186.
Jiménez, M., Romero, L., Domínguez, I.A., Espinosa, M.D.M., Domínguez, M., Dom, I.A. and Dom, M. (2019), “Additive manufacturing technologies: an overview about 3D printing methods and future prospects”, Complexity, Vol. 2019, doi: 10.1155/2019/9656938.
Kafle, A., Luis, E., Silwal, R., Pan, H.M., Shrestha, P.L. and Bastola, A.K. (2021), “3D/4D printing of polymers: fused deposition modelling (FDM), selective laser sintering (SLS), and stereolithography (SLA)”, Polymers, Vol. 13 No. 18, p. 3101, doi: 10.3390/POLYM13183101.
Karamimoghadam, M., Dezaki, M.L., Zolfagharian, A. and Bodaghi, M. (2023), “Influence of post-processing CO2 laser cutting and FFF 3D printing parameters on the surface morphology of PLAs: statistical modelling and RSM optimisation”, International Journal of Lightweight Materials and Manufacture, Vol. 6 No. 2, pp. 285-295, doi: 10.1016/J.IJLMM.2023.01.004.
Khaleghi, S., Dehnavi, F.N., Baghani, M., Safdari, M., Wang, K. and Baniassadi, M. (2021), “On the directional elastic modulus of the TPMS structures and a novel hybridization method to control anisotropy”, Materials & Design, Vol. 210, p. 110074, doi: 10.1016/J.MATDES.2021.110074.
Kumar, A. and Chhabra, D. (2022), “Adopting additive manufacturing as a cleaner fabrication framework for topologically optimized orthotic devices: implications over sustainable rehabilitation”, Cleaner Engineering and Technology, Vol. 10, pp. 1-15, doi: 10.1016/J.CLET.2022.100559.
Kumar, A., Verma, S. and Jeng, J.Y. (2020), “Supportless lattice structures for energy absorption fabricated by fused deposition modeling”, 3D Printing and Additive Manufacturing, Vol. 7 No. 2, pp. 85-96, doi: 10.1089/3dp.2019.0089.
Lee, H., Eom, R.I. and Lee, Y. (2019), “Evaluation of the mechanical properties of porous thermoplastic polyurethane obtained by 3D printing for protective gear”, Advances in Materials Science and Engineering, Vol. 2019, doi: 10.1155/2019/5838361.
Lee, S.H., Park, J.S., Jung, B.K. and Lee, S.A. (2016), “Effects of different seat cushions on interface pressure distribution: a pilot study”, Journal of Physical Therapy Science, Vol. 28 No. 1, p. 227, doi: 10.1589/JPTS.28.227.
Lopes, J.S.S., Machado, A.F., Micheletti, J.K., Almeida, A.C., Cavina, A.P. and Pastre, C.M. (2019), “Effects of training with elastic resistance versus conventional resistance on muscular strength: a systematic review and meta-analysis”, SAGE Open Medicine, Vol. 7, p. 205031211983111, doi: 10.1177/2050312119831116.
Lu, W., He, W., Wu, J. and Zhang, Y. (2022), “A critical review of additive manufacturing technology in rehabilitation medicine via the use of visual knowledge graph”, Virtual and Physical Prototyping, Vol. 18 No. 1, pp. 1-26, doi: 10.1080/17452759.2022.2132265.
Ma, Z., Lin, J., Xu, X., Ma, Z., Tang, L., Sun, C., Li, D., Liu, C., Zhong, Y. and Wang, L. (2019), “Design and 3D printing of adjustable modulus porous structures for customized diabetic foot insoles”, International Journal of Lightweight Materials and Manufacture, Vol. 2 No. 1, pp. 57-63, doi: 10.1016/j.ijlmm.2018.10.003.
Mahbod, M. and Asgari, M. (2019), “Elastic and plastic characterization of a new developed additively manufactured functionally graded porous lattice structure: analytical and numerical models”, International Journal of Mechanical Sciences, Vol. 155, pp. 248-266, doi: 10.1016/J.IJMECSCI.2019.02.041.
Martins, W.R., Carvalho, R.S., Silva, M.S., Blasczyk, J.C., Araújo, J.A., Carmo, J.D., Rodacki, A.L.F. and de Oliveira, R.J. (2014), “Mechanical evaluation of elastic tubes used in physical therapy”, Physiotherapy Theory and Practice, Vol. 30 No. 3, pp. 218-222, doi: 10.3109/09593985.2013.845806.
Maskery, I., Hussey, A., Panesar, A., Aremu, A., Tuck, C., Ashcroft, I. and Hague, R. (2017), “An investigation into reinforced and functionally graded lattice structures”, Journal of Cellular Plastics, Vol. 53 No. 2, pp. 151-165, doi: 10.1177/0021955X16639035.
Momeni, K., Mofidian, S.M.M. and Bardaweel, H. (2019), “Systematic design of high-strength multicomponent metamaterials”, Materials & Design, Vol. 183, p. 108124, doi: 10.1016/j.matdes.2019.108124.
Moradi, M., Aminzadeh, A., Rahmatabadi, D. and Rasouli, S.A. (2021), “Statistical and experimental analysis of process parameters of 3D nylon printed parts by fused deposition modeling: response surface modeling and optimization”, Journal of Materials Engineering and Performance, Vol. 30 No. 7, pp. 5441-5454.
Nazir, A., Gokcekaya, O., Billah, K., Ertugrul, O., Jiang, J., Sun, J. and Hussain, S. (2023), “Multi-material additive manufacturing: a systematic review of design, properties, applications, challenges, and 3D printing of materials and cellular metamaterials”, Materials & Design, Vol. 226, p. 111661, doi: 10.1016/J.MATDES.2023.111661.
Niknam, H. and Akbarzadeh, A.H. (2020), “Graded lattice structures: simultaneous enhancement in stiffness and energy absorption”, Materials & Design, Vol. 196, p. 109129, doi: 10.1016/j.matdes.2020.109129.
Orozco, P.S.P., Haro, F.B., Quintana, P.C., Pedro, A.B.S., D’Amato, R. and Juanes, J.A. (2019), “Aesthetics in orthopedic products: applications of the advanced manufacture (AM) to the industrial design of orthoses”, ACM International Conference Proceeding Series, pp. 372-379, doi: 10.1145/3362789.3362826.
Pham, M.S., Liu, C., Todd, I. and Lertthanasarn, J. (2019), “Damage-tolerant architected materials inspired by crystal microstructure”, Nature, Vol. 565 No. 7739, pp. 305-311, doi: 10.1038/s41586-018-0850-3.
Popescu, D., Zapciu, A., Amza, C., Baciu, F. and Marinescu, R. (2018), “FDM process parameters influence over the mechanical properties of polymer specimens: a review”, Polymer Testing, Vol. 69, pp. 157-166, doi: 10.1016/J.POLYMERTESTING.2018.05.020.
Prajapati, M.J., Bhat, C., Kumar, A., Verma, S., Lin, S.C. and Jeng, J.Y. (2022a), “Supportless lattice structure for additive manufacturing of functional products and the evaluation of its mechanical property at variable strain rates”, Materials, Vol. 15 No. 22, p. 7954, doi: 10.3390/MA15227954.
Prajapati, M.J., Kumar, A., Lin, S.C. and Jeng, J.Y. (2022b), “Multi-material additive manufacturing with lightweight closed-cell foam-filled lattice structures for enhanced mechanical and functional properties”, Additive Manufacturing, Vol. 54, p. 102766, doi: 10.1016/J.ADDMA.2022.102766.
Rahmatabadi, D., Soltanmohammadi, K., Aberoumand, M., Soleyman, E., Ghasemi, I., Baniassadi, M., Abrinia, K., Bodaghi, M. and Baghani, M. (2023a), “Development of pure poly vinyl chloride (PVC) with excellent 3D printability and macro- and micro-structural properties”, Macromolecular Materials and Engineering, Vol. 308 No. 5, p. 2200568, doi: 10.1002/MAME.202200568.
Rahmatabadi, D., Soltanmohammadi, K., Pahlavani, M., Aberoumand, M., Soleyman, E., Ghasemi, I., Baniassadi, M., Abrinia, K., Bodaghi, M. and Baghani, M. (2023b), “Shape memory performance assessment of FDM 3D printed PLA-TPU composites by box-behnken response surface methodology”, The International Journal of Advanced Manufacturing Technology, Vol. 127 Nos 1/2, pp. 935-950, doi: 10.1007/S00170-023-11571-2/TABLES/8.
Rodríguez-Parada, L., Rosa, S. and Mayuet, P.F. (2021), “Influence of 3D-Printed TPU properties for the design of elastic products”, Polymers, Vol. 13 No. 15, p. 2519, doi: 10.3390/POLYM13152519.
Rosa, S.D., Mayuet, P.F., Ramón, J., Salgueiro, M. and Rodríguez-Parada, L. (2021a), “Design of customized TPU lattice structures for additive manufacturing: influence on the functional properties in elastic products”, Polymers, Vol. 13 No. 24, p. 4341, doi: 10.3390/POLYM13244341.
Rosa, S.D., Mayuet, P.F. and Rodríguez, L. (2021b), “An overview of the additive manufacturing capabilities in the development of rehabilitation products with customized elastic properties”, IOP Conference Series: Materials Science and Engineering, Vol. 1193 No. 1, p. 12122, doi: 10.1088/1757-899X/1193/1/012122.
Santos, S., Soares, B., Leite, M. and Jacinto, J. (2017), “Design and development of a customised knee positioning orthosis using low cost 3D printers”, Virtual and Physical Prototyping, Vol. 12 No. 4, pp. 322-332, doi: 10.1080/17452759.2017.1350552.
Sha, Y., Jiani, L., Haoyu, C., Ritchie, R.O. and Jun, X. (2018), “Design and strengthening mechanisms in hierarchical architected materials processed using additive manufacturing”, International Journal of Mechanical Sciences, Pergamon, Vol. 149, pp. 150-163, doi: 10.1016/J.IJMECSCI.2018.09.038.
Sharma, S., Singh, J., Kumar, H., Sharma, A., Aggarwal, V., Gill, A.S., Jayarambabu, N., Kailasa, S. and Venkateswara Rao, K. (2020), “Utilization of rapid prototyping technology for the fabrication of an orthopedic shoe inserts for foot pain reprieve using thermo-softening viscoelastic polymers: a novel experimental approach”, Measurement and Control, Vol. 53 Nos 3/4, pp. 519-530, doi: 10.1177/0020294019887194/ASSET/IMAGES/LARGE/10.1177_0020294019887194-FIG11.JPEG.
Srivastava, V. and Gaur, H. (2020), “Revolutionary development in orthopedic insole by additive manufacturing”, Journal of Critical Review, Vol. 7 No. 4, p. 1943.
Tafazoli, M. and Nouri, M.D. (2022), “Experimental and numerical study and multi-objective optimisation of quasi-static compressive test on three-dimensional printed lattice-core sandwich structures”, International Journal of Crashworthiness, Vol. 27 No. 1, pp. 117-127, doi: 10.1080/13588265.2020.1775053.
Tang, Y., Dong, G., Xiong, Y. and Wang, Q. (2021), “Data-driven design of customized porous lattice sole fabricated by additive manufacturing”, Procedia Manufacturing, Vol. 53, pp. 318-326, doi: 10.1016/J.PROMFG.2021.06.035.
Tang, L., Wang, L., Bao, W., Zhu, S., Li, D., Zhao, N. and Liu, C. (2019), “Functional gradient structural design of customized diabetic insoles”, Journal of the Mechanical Behavior of Biomedical Materials, Vol. 94, pp. 279-287, doi: 10.1016/J.JMBBM.2019.03.003.
Texis (2024), “Texis - connected pressure mapping textile for healthcare applications”, available at: www.texisense.com/ (accessed 13 November 2023).
Tsang, H.H., Tse, K.M., Chan, K.Y., Lu, G. and Lau, A.K.T. (2019), “Energy absorption of muscle-inspired hierarchical structure: experimental investigation”, Composite Structures, Vol. 226 No. May, p. 111250, doi: 10.1016/j.compstruct.2019.111250.
Wang, C., Gu, X., Zhu, J., Zhou, H., Li, S. and Zhang, W. (2020a), “Concurrent design of hierarchical structures with three-dimensional parameterized lattice microstructures for additive manufacturing”, Structural and Multidisciplinary Optimization, Vol. 61 No. 3, pp. 869-894, doi: 10.1007/s00158-019-02408-2.
Wang, L., Kang, J., Sun, C., Li, D., Cao, Y. and Jin, Z. (2017), “Mapping porous microstructures to yield desired mechanical properties for application in 3D printed bone scaffolds and orthopaedic implants”, Materials & Design, Vol. 133, pp. 62-68, doi: 10.1016/J.MATDES.2017.07.021.
Wang, Y., Tan, Q., Pu, F., Boone, D. and Zhang, M. (2020b), “A review of the application of additive manufacturing in prosthetic and orthotic clinics from a biomechanical perspective”, Engineering, Vol. 6 No. 11, pp. 1258-1266, doi: 10.1016/j.eng.2020.07.019.
Wang, M., Zhang, J. and Wang, W. (2022), “Compression and deformation behaviors of hierarchical circular-cell lattice structure with enhanced mechanical properties and energy absorption capacity”, Aerospace, Vol. 9 No. 12, doi: 10.3390/aerospace9120786.
Wheelchair (2024), “Wheelchair cushion vicair vector O2”, available at: www.vicair.com/product/wheelchair-cushion-vicair-vector-o2-10cm/ (accessed 12 November 2023).
Xiao, J. and Gao, Y. (2017), “The manufacture of 3D printing of medical grade TPU”, Progress in Additive Manufacturing, Vol. 2 No. 3, pp. 117-123, doi: 10.1007/S40964-017-0023-1.
Yan, W., Ding, M., Kong, B., Xi, X.B. and Zhou, M. (2019), “Lightweight splint design for individualized treatment of distal radius fracture”, Journal of Medical Systems, Vol. 43 No. 8, pp. 1-10, doi: 10.1007/s10916-019-1404-4.
Yang, J., Cheng, Y., Gong, X., Yi, S., Li, C.W., Jiang, L. and Yi, C. (2022), “An integrative review on the applications of 3D printing in the field of in vitro diagnostics”, Chinese Chemical Letters, Vol. 33 No. 5, pp. 2231-2242, doi: 10.1016/J.CCLET.2021.08.105.
Acknowledgements
This research was supported by the Puerta del Mar University Hospital in Cádiz, which provided knowledge, experience, as well as the loan of pressure blanket equipment.